Re-Designing Thermal Fuses with VOITH
Together, we conceptualized replacement options for a thermal fuse that is used in large coupling casings and evaluated them under cost and functional aspects.
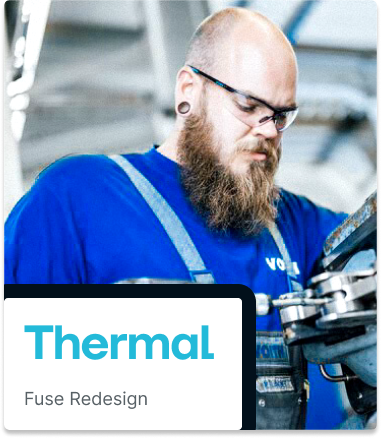
This is a great example of paying attention to detail. Although the fuse is just a small part of the final product, Voith didn't shy away from diving deep into the creative process. By challenging inherent assumptions, we arrived at simple, yet smart options that avoid harmful materials altogether.
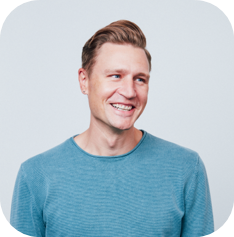
Our Final Result
Overview
Challenge
Solution
Technologies
Impact
Our Final Result
A fully sustainable alternative solution to replace the current chemical compound, evaluated from a cost and functionality perspective.
Ideating & evaluating sustainable alternatives for a thermal fuse
- Retaining performance and cost while optimising for sustainability
- Technological ideation using a morphological analysis
- Creative hardware ideation under constraints
Due to a change in legislation, a new thermal fuse used for large coupling casings in heavy machinery had to be redesigned.
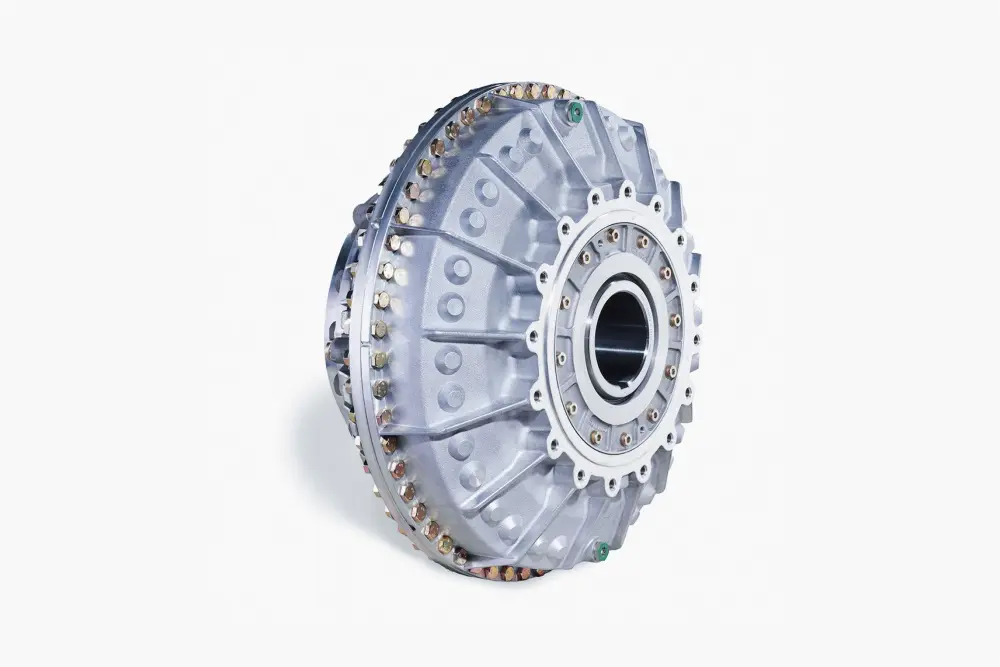
Looking for an
Innovation Partner?
Contact UsChallenge
The current thermal fuse utilized chemical compounds soon to be banned by EU legislation, a different, and sustainable option was required.
Adapting to New Legal Requirements
This posed multiple engineering challenges. The new fuse had to be fast acting, in a narrow temperature band while at the same time withstanding the strains and abuse in often rough mining environments.
Solution
A sustainable thermal fuse that provides comparable release performance without increasing costs.
All About VOITH
Innovation for Drive Technology, Hydropower, and Papermaking
The family owned Voith Group is a global technology supplier with a broad portfolio of systems, products, services, and digital applications. Voith operates in the energy, paper, mining, and transport & automotive markets. Research and development traditionally have a high priority at Voith – the company holds several thousand active patents.
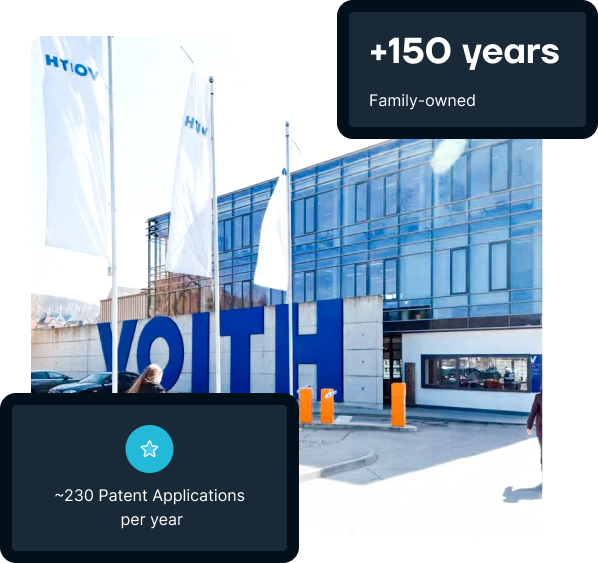
Tackling the Challenge in a Four-Step Process
Definition of Requirements and Constraints
In a workshop we considered and discussed the surrounding aspects the new solution needs to comply with. This included different use cases, environmental/thermal conditions, users and other operating constraints.
Ideation and Research
With a deep understanding of the usage situation, we used a number of creative techniques to elicit several dozen ideas. Particularly uncovering latent assumptions and turning those on their heads led to several fruitful directions for alternative operating principles. Morphological analysis was used to separate sub-functions, such as retaining pressure at certain temperatures while releasing it at others, and to ideate functional replacement options.
Testing
After re-combining and evaluating the resulting ideas for functionality, anticipated costs, sustainability, and manufacturability, we arrived at three alternative concepts. Some merely replaced the soldering materials, others built on completely new mechanical release mechanisms.
Prototype
Using a simple yet realistic testing setup, the resulting concepts have since undergone the first prototype tests. Two solutions stand out – one for its simplicity and use of the current fuse design with merely an alternative solder; the other for its use of an alternative bursting mechanism, which has been adapted from its current use in sprinkler systems.